研润企业硬度计技术新闻中心
- 上海研润光机科技有限公司前身是国家仪器技
- 术研究所,成立于2005年,是一家以研发、
- 生产、非标定制自动化生产检测设备,计算机
- 软件开发为主的高新技术企业。主导产品:材
- 料仪器、光学仪器、自动化生产检测设备等。
- 硬度计技术新闻
- 洛氏硬度计技术新闻
- 维氏硬度计技术新闻
- 布氏硬度计技术新闻
- 显微硬度计技术新闻
4008127833/021-58391850
扫一扫关注我们
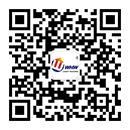
|
|
|
你尝试过缩短加热时间来优化热处理工艺吗? |
本站文字和内容版权为上海研润光学显微硬度计显微硬度计制造厂所有http://www.yr1718.net;转载请注明出处 |
热处理是大量耗能的加工过程,缩短热处理加热时间是节能的有效方法之一。碳钢和低合金钢施行零保温加热、亚共析钢加热到F+A两相区的不完全淬火都是可行的。1.零保温淬火工艺零保温时间,即取消或缩短结构钢的加热保持时间。对于碳素钢和低合金钢的单件加热升温,当炉子温度到达工艺指定温度即工件表面到达工艺温度时,工件即已透烧,而无需再额外增加透烧时间,这就是所说的“零”保温淬火。对碳钢和低碳合金钢,如果产品形状比较简单,尺寸相对较小零件,完全可以采用零保温淬火,以达到高效节能的目的,既可以保证产品质量,以免过热过烧、氧化脱碳,又可以大大避免耗时、耗能的现象。应用实例1:45钢锥齿轮零保温淬火工艺锥齿轮,外形尺寸为φ32.93mm×20mm,内孔直径φ10mm,材料为45钢,要求调质硬度220~250HBW,齿部高频淬火硬度40~46HRC。(1)原加工工艺路线。锻坯→正火→粗车→调质→机加工→高频淬火→磨削内孔,由于加工工序繁多,成本高。对此,取消正火和调质工序,直接进行淬火,不仅保证了产品质量,而且降低了生产成本。(2)零保温淬火工艺及效果。(840±10)℃箱式炉加热,保温2min,水淬油冷;(320±10)℃保温1h回火。经检查齿部硬度41~44HRC,经磁粉探伤检查,未发现淬火裂纹,这是由于齿轮在(840±10)℃加热时,齿表面快速升温,齿心部还处于相变点以下,这时淬火避开了45钢淬火裂纹的危险尺寸,且变形小。其次,水淬油冷淬火方式,减小了淬火应力,减少了淬火开裂倾向。零保温淬火时,齿表面保温时间几乎是零,因而晶粒细小。用此工艺处理的3000余件齿轮,未发现一件裂纹,经抽查,硬度全部合格。应用实例2:零保温正火工艺内燃机中28种精铸零件要进行正火或调质处理。这些精铸零件具有以下特点:批量大,每年处理零件二百多万件;重量轻,单件重量0.021~1.33kg;材质均为ZG310-570;图样只有硬度要求。(1)原正火工艺。原正火是按传统的加热公式τ=KαD计算加热时间,式中K=2.0,α=1.4~1.8,故加热时间长、耗电量大。精铸热处理工件每吨耗电量为1052kW·h/t。(2)新工艺。通过多次试验和反复生产验证,K值确定为1.4~1.8,后制订了箱式炉中多层散装堆料加热时间计算公式:τ=(1.4~1.8)×(10+0.6D+0.2G)。式中,K为加热时的修正系数;D为工件的有效厚度(mm);G为工件装炉总重量(kg)。(3)节能效果。经新、老工艺方案的经济效益如表1所示。28种内燃机零件热处理平均每吨耗电量从1020.59kW·h/t,下降到451.13kW·h/t,达到了节电54.83%的效果,工时节约56.13%,年节电18万多元,年节约工时近9000h。因此,经济效益巨大。表1 新、老工艺各类技术经济指标对比零件名称工艺装炉量每炉加热时间/min年耗电量/kW·h年节约工时/h年节约电量/kW·h/件/kg曲轴带轮新老15080177941051353949195135269855644曲轴起动爪新老50027517084110110124092253349010124气门摇臂新老10003501655811011049621141721446492100液压泵出油管凸缘新老25007001383975803407128704589463分离杆支架新老280070012632758045421930571514763合计—————88251820942.减小加热时间计算系数的方法热处理工艺选择不当,加热和保温时间的计算过于保守,将会造成能源浪费。大连圣洁公司通过十几年的研究、试验,总结了用于热处理加热时保温时间的简单计算法则——369法则。实际生产表明,该法则的实施有助于节约能源、降低生产成本、提高产品质量和生产效率。(1)各种金属材料在空气炉中加热淬火保温的369法则①碳素钢和低合金钢(45、T7、T8等)。传统的碳素钢淬火加热时间的计算公式:τ=KαD。式中τ为加热时间(min),K为反映装炉状况的修正系数,通常在1.0~1.3范围内选取;α为加热系数,一般在0.7~0.8min/mm;D为工件有效厚度(mm)。按369法则,对于碳素钢和低合金钢,保温时间仅需传统保温时间30%即可。应用实例1:采用箱式炉加热φ60mm的45钢工件,其淬火保温时间共需60min×30%=18min。实际上,在炉温仪表指示的温度到温后,按工件每3mm有效厚度透烧时间为1min即足够。②合金结构钢(40Cr、40MnB、35CrMo等)。按369法则,合金结构钢加热的保温时间可以是原来传统保温时间的60%。应用实例2:用传统的公式计算的40Cr的保温时间如果为100min,按369法则,新的保温时间为:100min×60%=60min。③高合金工具钢(9SiCr、CrWMn、Cr12MoV、W6、W8等)。按369法则的保温时间是原来传统保温时间的90%。④特殊性能钢(不锈钢、耐热钢、耐磨钢等)。这些钢种的369法则可按照合金工具钢的公式计算,即以传统公式计算的加热保温时间×90%作为保温时间。⑤预热淬火。对于大型工件(有效直径≥1m)调质处理的预热保温时间的369法则为:T1=3D;T2=6D;T3=9D。式中:T1为次预热时间(h);T2为第二次预热时间(h);T3为终保温时间(h);D为工件的有效厚度(m)。实际生产证明,对于空气炉加热的中、小零件(有效尺寸≤500mm),预热和加热时的保温时间也可以按369法则计算。(2)真空加热保温时的369法则。传统的真空炉加热保温时间的计算公式如下:T1=30+(1.5~2)D;T2=30+(1.0~1.5)D;T3=20+(0.25~0.5)D。式中:T1为次预热时间(min);T2为第二次预热时间(min);T3为终保温时间(min);D为工件的有效厚度(mm)。按369法则1,装炉量在100~200kg,工件有效尺寸在100mm左右时,按下式计算:T真1=T真2=T真3=0.4×G+D。式中:G为装炉工件净重量(kg),其他符号意义与上述相同。按369法则2,工件尺寸基本相同,摆放整齐,并留有一定空隙(摆放空隙<D)时,按下式计算:G≤300kg:T真1=T真2=T真3=30+D;G=301~600kg:T真1=T真2=T真3=(30~60)+D;G≥901kg:T真1=T真2=T真3=90+D。式中:G为装炉总重量(kg),包括工件、料筐、料架及料盘的所有重量;D为工件有效直径(mm)。在实际生产过程中,对于变形要求严格的工模具,次预热时间应取上限值,第二次预热取中限值,终热处理取下限值。对于普通合金结构钢工件或变形要求不太严格的工件,次预热的时间可以取下限值,而在终加热时取上限值。对于一次仅装一件的大型工件,次与第二次预热时间可以取下限,终加热时,则根据实际要求取中限或上限值。(3)密封箱式多用炉的369法则。工件在密封箱式炉中加热的热效率比真空炉高,故其369法则的参数可以按真空炉369法则中的下限选取,即:G=301~600kg:T真1=T真2=T真3=30+D;G=601~900kg:T真1=T真2=T真3=60+D;G≥901kg:T真1=T真2=T真3=90+D。式中G、D符号意义同369法则2。3.高温渗碳工艺工件渗碳淬火量大、面广、耗能大,是热处理行业提高节能效果突破口之一。对部分要求深层渗碳工件采用高温渗碳工艺,如1010℃以上高温渗碳,可比在930℃常规渗碳工艺时间缩短30%~50%,因此显著降低能源消耗和生产成本。应用实例:高温可控气氛渗碳工艺齿轮轴,材料为20CrMnTi钢,渗碳层深度要求为4mm,要求渗碳、淬火与回火。(1)传统渗碳工艺。渗碳、淬火原采用井式气体渗碳炉,按照传统渗碳工艺(见图1)生产时,总工艺时间为73h,该工艺特点是生产周期长、成本高。(2)高温渗碳工艺与节能效果。现渗碳采用QS6110-H型高温可控气氛多用炉,齿轮轴高温渗碳工艺见图2所示,渗碳总工艺时间为16h。同传统工艺相比,渗碳时间缩短57h,节能60%以上,提高设备生产能力2倍以上。4.化学催渗技术化学热处理是一种周期长、效率低、耗能大的工艺。热处理工作者通过试验发现,某些化学物质(如稀土化合物、氯化物等)对渗碳、碳氮共渗、渗氮等化学热处理具有催渗作用,通过催渗,可缩短热处理时间、提高生产效率、降低生产成本,是一条十分有效的节能途径。(1)氧化腐蚀催渗技术。该工艺主要有表面预氧化法和化学腐蚀法。化学腐蚀法是在渗氮、碳时通过在渗剂或气氛中添加强腐蚀性物质,如氯化物、氟化物以及碘化物等来实现催渗。应用实例:用工业纯NH4Cl作催渗剂。将NH4Cl粉末溶于工业酒精(一般按每立方米炉内容积加入130~150g的NH4Cl计算)。图3为在RQ3-75-9型井式渗碳炉内进行的催渗气体氮碳共渗工艺。节能效果:①NH4Cl催渗氮碳共渗与气体渗氮后渗层深度与硬度对比如表2所示;②同普通渗氮工艺相比,NH4Cl催渗氮碳共渗可节省时间50%以上,即相应节省了电能,该工艺操作简便,安全可靠。表2催渗氮碳共渗与气体渗氮结果对比钢号普通气体渗氮催渗氮碳共渗温度/℃时间/h渗氮层深度/mm表面硬度HV温度/℃时间/h渗氮层深度/mm表面硬度HV38CrMoAl520±5570±5530±51016180.4~0.6>1000560±1010~150.4~0.6≥100040Cr480±10500±102015~200.3~0.5≥600560±10100.3~0.5≥60018Cr2Ni4WA490±10300.2~0.3≥600560±10100.3~0.4≥600(2)稀土催渗技术。在化学热处理中,在渗剂中添加一定的稀土元素,利用稀土元素的催化作用实现催渗过程,可显著缩短化学热处理周期。如在渗碳温度不变情况下,可以提高渗碳速度15%~25%,提高生产效率20%左右,节能20%左右。应用实例1:连续式渗碳炉稀土快速渗碳工艺我公司生产的CA-457型“解放”牌重载汽车后桥从动弧齿锥齿轮,外形尺寸为φ457mm×62mm,材料为20CrMnTiH3钢,技术要求:渗碳淬硬层深度1.70~2.10mm,表面与心部硬度分别为58~63HRC和35~40HRC,碳化物1~5级,马氏体及残余奥氏体1~5级。齿轮渗碳淬火及回火采用双排连续式渗碳自动生产线,每盘装6件齿轮,其工艺路线为:450~500℃预处理→880~900℃预热(1区)→920~925℃预渗碳(2区)→925~930℃渗碳(3区)→890~910℃扩散(4区)→840~850℃预冷(5区)→870℃保温室压床淬火→60~70℃清洗→180℃×6h回火→喷丸清理→交检。原渗碳工艺与稀土快速渗碳工艺参数对比见表3。通过表3可以看出,采用稀土渗碳工艺后,推料周期由原工艺38min缩短至30min,每一盘齿轮在炉内加热时间减少6h,提高渗碳速度20%,即提高热处理生产效率20%。表3原渗碳工艺与稀土快速渗碳工艺参数对比工艺原渗碳工艺稀土快速渗碳工艺加热区段1234512345炉温/℃880920930900860880920930890860设定碳势Cp(%)—1.051.201.05~1.100.95~1.00—1.251.301.00~1.050.95~1.00甲醇/(mL/min)202020253002020200稀土甲醇/(mL/min)0000002030100氮气/(m3/h)1.21.41.61.82.022223丙烷气/(m3/h)00.30.40000.50.40.050推料周期/min3830表4项目实施前后单位物料及用电消耗情况原渗碳工艺消耗物电能/kW·h丙烷气/kg甲醇/kg稀土/L每公斤单耗2.040.00650.0380费用(元)1.430.0410.1450稀土快速渗碳工艺消耗物电能/kW·h丙烷气/kg甲醇/kg稀土/L每公斤单耗1.730.00580.0330.0004费用(元)1.210.0370.128200节能效果:表4为项目实施前后单位物料及用电消耗情况。按同比产品产量2000t/年计算,每年可降低能耗65万kW·h,同时减少渗碳剂的消耗。因此,该工艺节能、降耗效果显著。应用实例2:球墨铸铁稀土催渗氮碳共渗球墨铸铁由于含碳量高,氮碳共渗时间长,生产效率低,成本高,渗层深度不均,表面硬度低,变形超差。加入稀土元素催渗,提高了产品质量和生产效率。气体低温氮碳共渗在RN-60-6A型井式气体渗氮炉中进行,S195型柴油机球墨铸铁曲轴每炉114根,(560±10)℃×2h,通入氨气滴注乙醇,稀土加入量为15g,出炉空冷。应用效果:经检验,加入15g稀土后,氮碳共渗层深度0.10mm,表面硬度450HV,炉次合格率100%。当共渗层深度要求在0.12mm时,常规氮碳共渗需4.5h,而加入15g稀土后仅需2h。(3)BH催渗技术。BH催渗剂中含有一种新的化学物质,它可以改变渗剂的分解过程,促使渗剂充分分解,加快扩散速度。采用温度不变、提高渗碳速度的催渗工艺,可以提高效率25%,一台多用炉每年可增加产值80多万元。应用实例:BH催渗工艺齿轮BH催渗工艺。二汽东风精工齿轮厂将BH催渗剂按1200的体积比例分别添加到煤油和甲醇中,在RQ3-105-9型井式渗碳炉中,对材料为20CrMo钢半轴齿轮进行渗碳,不同渗碳工艺如图4和图5所示。节能效果。50炉次试验结果见表5。由表5可知,采用BH催渗技术后生产效率提高了20%,每炉节电90kW·h,产品质量提高,且工艺稳定。表5采用不同渗碳工艺后50炉次对比检验结果工艺碳化物/级马氏体、残余奥氏体/级表面硬度HRC渗碳层深度/mm平均每炉周期/h炉均耗电/kW·h原工艺1~21~558~621.0~1.210.2360BH工艺1~21~458~621.05~1.158.12705.快速回火技术采用快速回火装置回火及淬火钢的高温快速回火,可以达到显著节能效果。(1)采用快速回火装置回火。德国材料技术研究所提出一种非等温快速回火的方法,在190℃回火10min可代替160℃回火2h。通过在加热气氛和工件之间采用高速对流、涌流等方式,设计更高效的热转换器促进加热可以显著减少回火时间,同时还能大大改善整个工件加热温度的均匀性。快速回火采用高精度加热炉,不仅要求回火炉温度均匀,而且传热也均匀。通过使用涡轮可以实现快速传热。在Pyro系统(Pyro回火软体集成了回火计算软件和Pyrograph热交换软体)中工件加热速度和温度均匀性得到了优化。快速回火装置应用:采用快速回火工艺能够显著提高热处理效率和工件性能,而且还可以节约地面空间。图6为汽车连接件用快速回火装置,工件回火周期为6~8min。图7为轿车及叉车后轴用快速回火装置,工件回火周期为20min。图6 汽车CV连接件用快速回火装置图7 轿车及叉车后轴用快速回火装置(2)淬火钢的高温快速回火工艺。淬火钢的高温快速回火是,淬火后的钢件在Ac1点以上温度,根据工件的厚度代入经验公式计算出所需回火时间,几十秒或几百秒的回火,可以达到按传统工艺在低温、中温和高温回火几小时的效果,节能显著。回火温度的选定:其选用的原则是,短时间的高温回火与长时间的低温回火达到相同的组织结构和力学性能。依据生产上对钢件性能的需要在Ac1以上某一温度,准确控制一定的回火时间,使其得到马氏体、托氏体和索氏体的组织,从而获得高的耐磨性、高的弹性极限和优良的综合力学性能。回火时间的确定:可用如下经验公式计算:T=Ks+AsD。式中,T为回火时间(s);Ks为回火时间基数(s),As为回火时间系数(s/mm),D为工件有效厚度(mm)。例如,45钢用高温快速回火时,温度为860℃,选用Ks=30s,As=0.3s/mm,D=10mm,则T=30+0.3×10=33(s),即高温回火时间为33s,回火后硬度为52HRC。若用传统工艺时,回火温度为200℃,回火后硬度为52HRC。应用实例:对40Cr、45及T10钢件采用高温箱式电阻炉加热回火,当炉温达到指定的温度后,根据所需力学性能(即硬度)按表6所给数据来确定保温时间。表6高温快速回火法和传统工艺回火法与时间对照表传统工艺回火高温快速回火回火温度/℃回火时间/s回火时间系数/(s/mm)回火温度/℃回火时间基数/s碳素钢合金钢20036000.30.3860302501.51.53002.42.43503.13.14003.83.84505.35.350078550911.36001015.36501217按照表6所给的数据和工件厚度,计算出回火时间,回火后就可以得出在不同时间回火后的力学性能,经与传统回火工艺所得力学性能对比,具有相近的力学性能。高温快速回火法不产生回火脆性,省时、节电。但对高合金钢和大件回火暂不适用。应用效果:对经纬纺织机上所用的Roll,以及一些传动的轴类零件的回火采用高温快速回火工艺,效果非常好,不仅达到了产品质量要求,而且节约了能源。6.用短时加热淬火代替渗碳淬火的方法应用实例:20钢轴承滚柱低碳马氏体强化代替渗碳工艺轴承滚柱原采用20钢渗碳淬火回火处理工艺,耗电大。现改为20钢920~940℃加热淬火,加热时间按35~40s/mm计算,淬入w(NaCl)=6%~10%水溶液,180℃×2h回火。硬度44~46HRC,工时缩短40%,成本降低20%。
|
合作站点:
合作站点:
合作站点:
合作站点:
|
|